Two-stroke engine: What are its pros and cons?
A two-stroke engine, also referred to as a two-stroke cycle, is a piston combustion engine working in two strokes.
This means that the working cycle of the engine will take place during two strokes of the piston and one revolution of the crankshaft.
Content
Two-stroke engine function
To be clear, the operation of a two-stroke engine also consists of four strokes, just like a four-stroke engine. However, several of them are running simultaneously. The reduction of the number of cycles from four to two is achieved by the space under the piston; thus, the crankcase also participates in the replacement of the cylinder filling.
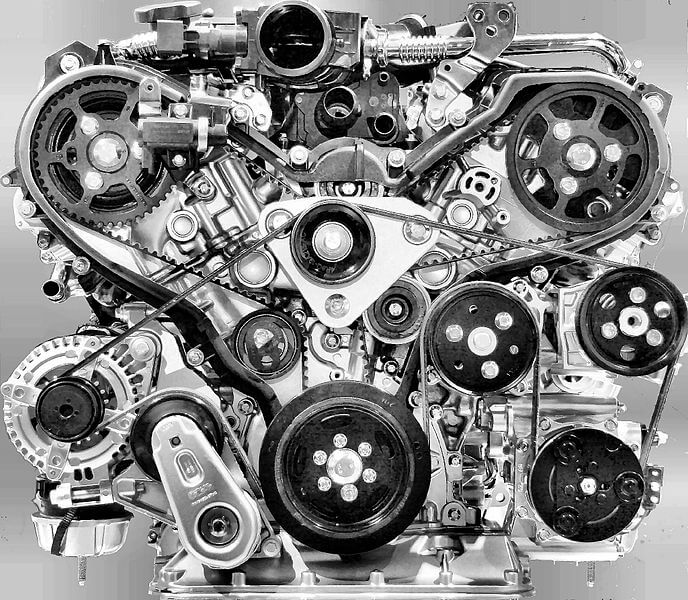
With a two-stroke engine, two work cycles co-occur, while one occurs in the space above the piston with combustion and the other under the piston without combustion.
A classic two-stroke engine does not contain a valve distribution and thus neither valves, camshaft, belt, or rockers. To replace the contents of the cylinder, three channels are used instead of valves, more precisely:
Intake channel – starts from the carburetor and leads to the crankcase
Discharge channel – connects the crankcase with the combustion chamber of the cylinder
Exhaust channel – opens from the combustion chamber of the cylinder into the exhaust pipe
Due to the absence of a valve train and its components, a two-stroke engine is smaller and lighter than other four-stroke engines with the same displacement and number of cylinders.
A two-stroke engine has a similar crankshaft to a four-stroke engine. During its movement from the top dead center to the bottom dead center, the piston ensures, among other things, pressure, fuel supply, and its transfer to the cylinder's combustion chamber.
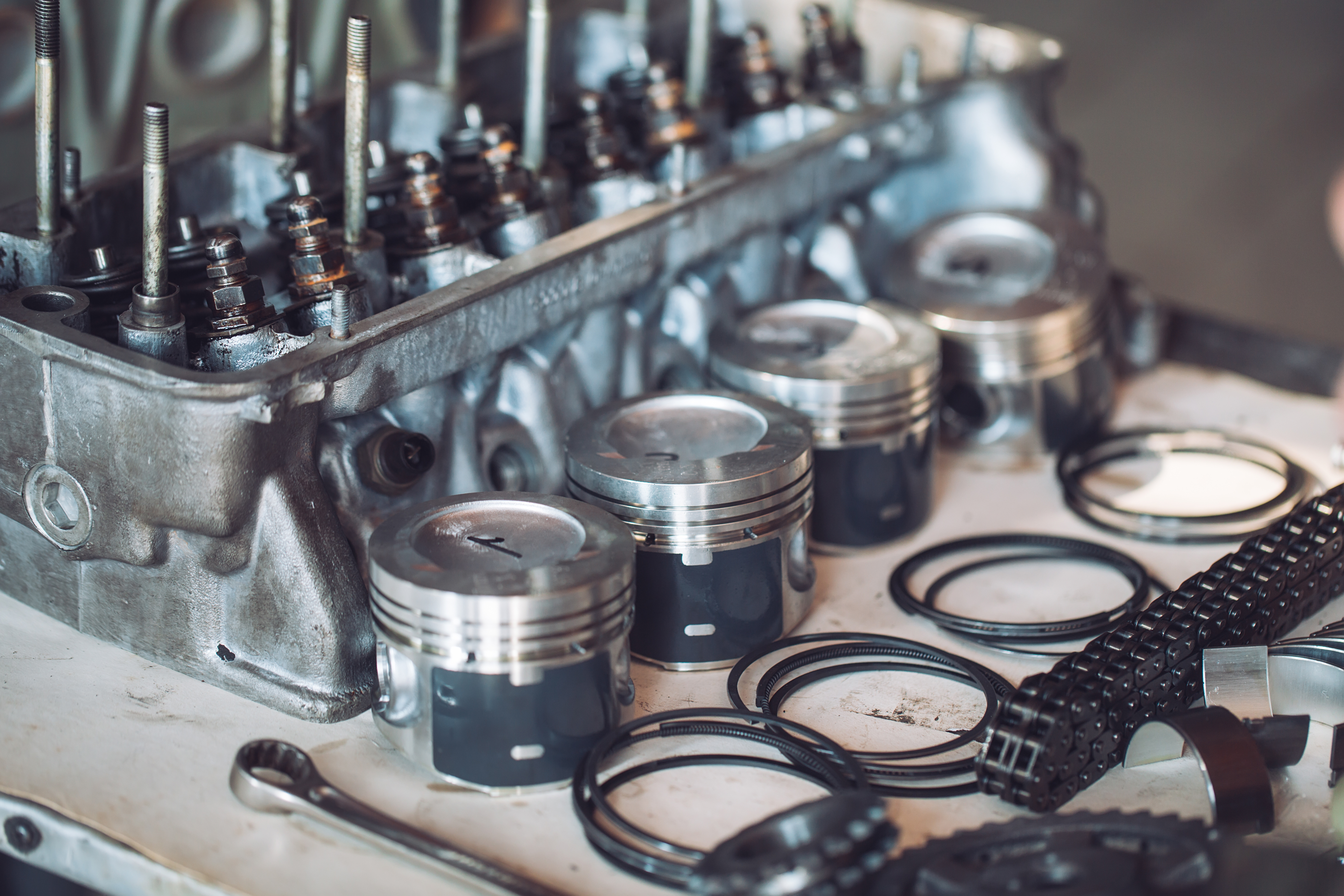
Engine Pistons: How do they work?
It works in such a way that the piston, when moving to its lower dead center, pushes fuel through the discharge channel up into the cylinder's combustion chamber. Subsequently, when moving to its upper dead center, it sucks in additional fuel through the suction channel under the piston or into the crankcase.
Engine lubrication:
With two-stroke engines, the engine's moving parts, such as crank or connecting rod bearings, are flooded with fuel, which means that they cannot be lubricated in a classic way as with four-stroke engines. However, in most cases, the fuel does not have sufficient lubrication capabilities, which is why oil is added to the fuel.
This lubrication is called grease lubrication and is the simplest way to lubricate the engine. In this type of lubrication, oil is added directly to the fuel, mixing it in an oil-to-fuel ratio ranging from approximately 1:20 to 1:100.
Two-stroke engine cycles
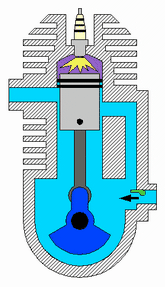
1. The first stroke of the piston (intake and compression):
The piston moves upward from its bottom dead center to its top dead center.
Above the piston:
During its movement from the bottom dead center to the top dead center, the piston first closes the discharge channel through which the mixture is pushed into the space above the piston. Subsequently, the piston also closes the exhaust channel, creating an isolated space in the cylinder, leading to the mixture's compression.
Under the piston:
After the piston has traveled about half its stroke, its lower edge opens the intake port. This will cause the ignition mixture from the carburetor to begin to be sucked into the crankcase. But that's not all.
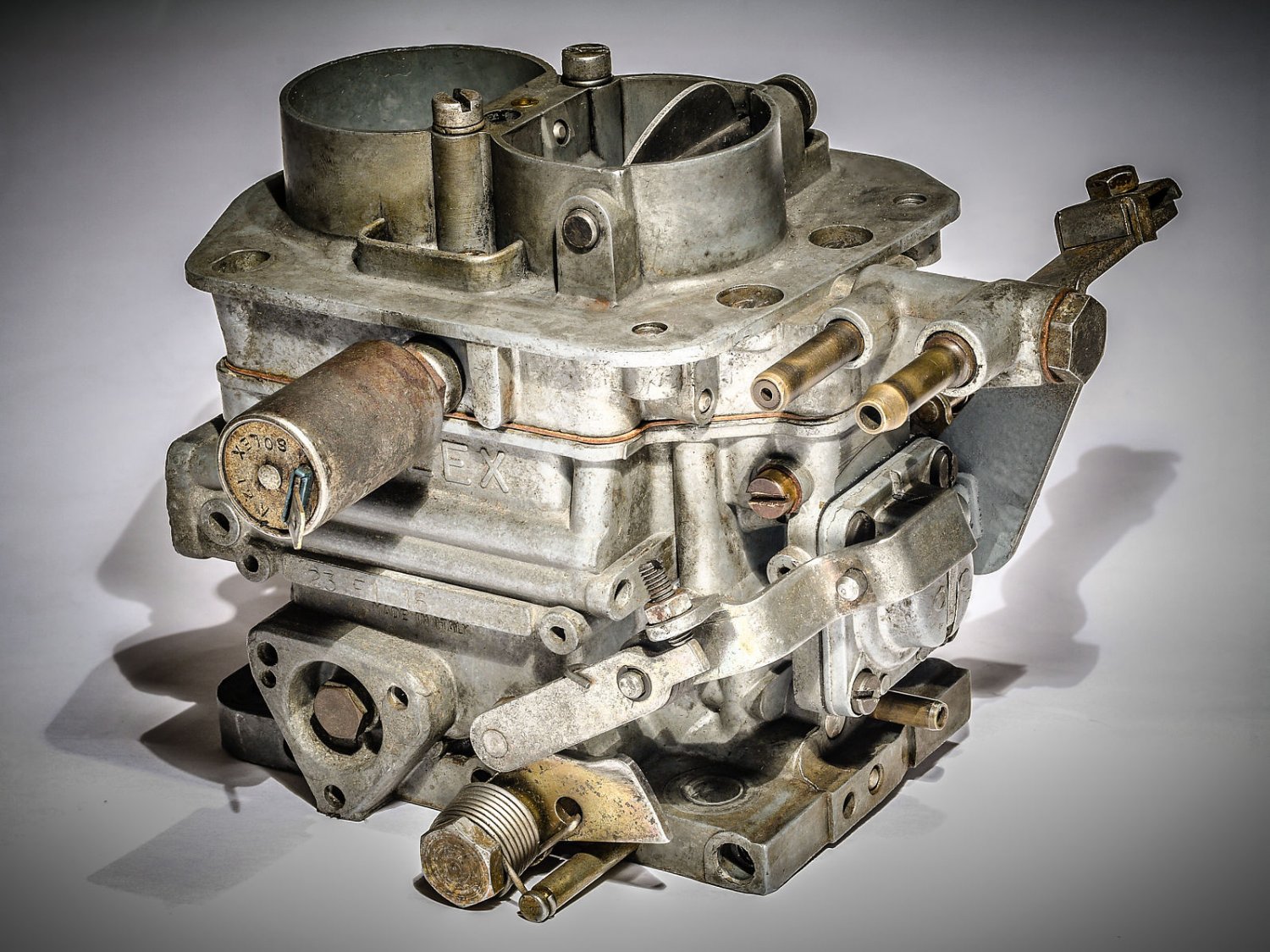
Carburetor: How does this device work?
Just before the top dead center of the piston, a spark jumps between the electrodes of the spark plug, which causes the ignition (ignition) of the mixture. Combustion creates thermal energy, which manifests itself by increasing the pressure in the cylinder, which moves the piston downwards and thus converts the thermal energy of the fuel into the mechanical work of the engine.
2. Second piston stroke:
The piston moves from its top dead center downwards to its bottom dead center.
Above the piston:
During the second stroke of the piston, expansion takes place in the space above the piston, which pushes the piston from the top dead center to the bottom dead center.
Under the piston:
An incendiary mixture is sucked into the crankcase through the open suction channel. After the piston has completed half of its stroke towards the bottom dead center, the intake port closes, compressing the mixture in the crankcase.
Just before the end of the expansion, the piston opens the exhaust port, which causes the pressure in the cylinder to drop. The piston opens the discharge channel, and the ignition mixture from the crankcase flushes the combustion gases out of the cylinder under pressure while filling it for the next engine work cycle.
Cylinder flushing
Cylinder flushing is a phase that does not occur in a four-stroke engine. However, it is extremely important for a two-stroke engine because its course significantly affects the engine parameters.
In four-stroke engines, it is common for exhaust gases to be forced out by the movement of the piston to the top dead center, but in the case of two-stroke engines, other factors must ensure the emptying of the cylinders, more precisely:
Free exhaust – flue gases get out of the cylinder through the exhaust channel only due to the differential pressure in the cylinder and the exhaust pipe.
Extrusion with a fresh charge - after the discharge valve opens, the ignition mixture begins to flow into the cylinder, pushing the combustion gases out.
The flushing phase is often limited to the time the discharge channel is open until the exhaust channel is closed.
However, with different engine modes, when flushing the cylinders, the following may occur:
More or less mixing of the fresh mixture with the exhaust gases, as their direct contact occurs
Leakage of the fresh mixture into the exhaust pipe
Insufficient flushing of the cylinder with a high residue of exhaust gases during the next engine work cycle
A two-stroke engine can be designed as a gasoline engine, but it can also be designed as a diesel engine.
Two-stroke diesel engine
The working principle of the two-stroke diesel engine is the same as that of the spark two-stroke engine. One significant difference is that the mixture is created only in the cylinder.
The fuel is thus injected into the cylinder just before the end of the compression due to the precise moment of ignition. Most two-stroke diesel engines use a classic valve for fuel injection, which is very similar to a four-stroke engine valve.
A supercharger is often used in two-stroke engines to create boost pressure. However, the possibility of supercharging the engine using a turbocharger or a combination of a turbocharger and a compressor is also an option.
Advantages of a two-stroke engine:
Simple construction
Lower weight compared to a four-stroke engine
Smaller engine dimensions
Absence of valve train
Lower production costs
Simple engine lubrication system
Cooling is, in most cases, air, so all parts of the water cooling system are eliminated
Possibility to work in any position (even upside down)
Maximum performance is achieved at lower revolutions, as each downward movement of the piston accompanies combustion
In some cases, it is easier to rev
Disadvantages of a two-stroke engine:
Unecological due to the mixing of oil into the fuel
High fuel consumption due to frequent leakage of the unburned mixture into the exhaust during flushing
Higher consumption of engine oil compared to a four-stroke engine
Irregular engine operation at low speeds
Higher engine noise
Mixing of burned and unburned mixture
Due to the location of the channels on the side of the cylinder, higher wear of the piston rings occurs.