Radial engine: Did you know what type of motor it is?
A radial engine is a reciprocating internal combustion engine with a single crankshaft, which has cylinders arranged in a circle (in one or more rows) perpendicular to the axis of the crankshaft so that all cylinders make the same angle with each other.
This article will explain how the radial engine works, its use, and a brief history.
Content
Use of a radial engine
A radial engine must have at least three cylinders (otherwise, it would be a boxer engine) and usually has an odd number of cylinders in one row. A radial engine with cylinders arranged in only one row is also a flat engine. If the cylinders are arranged in multiple planes, the radial engine is called, according to the number of rows, a two-, three-, four-cylinder radial engine, and so on.
This engine type is mainly used in aviation, but during the Second World War, it was also used in tanks. However, some madmen have installed a radial engine under a car's hood, which is why we will write something more about this engine.
The history of the radial engine in a nutshell
Danish engineer Jacob Ellrhammer built the first radial engine between 1903 and 1904. It was a three-cylinder radial engine that was air-cooled.
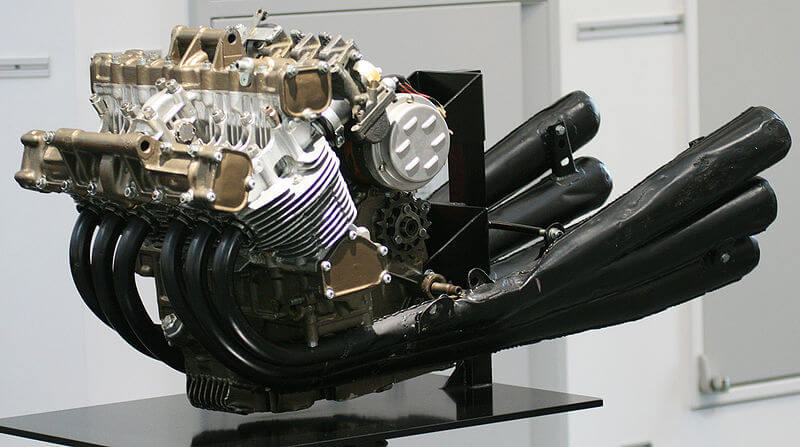
Most radial engines are air-cooled, but among the most successful early radial engines, we can include the 9-cylinder liquid-cooled engines manufactured by Salmson Moteurs from 1908 until 1920.
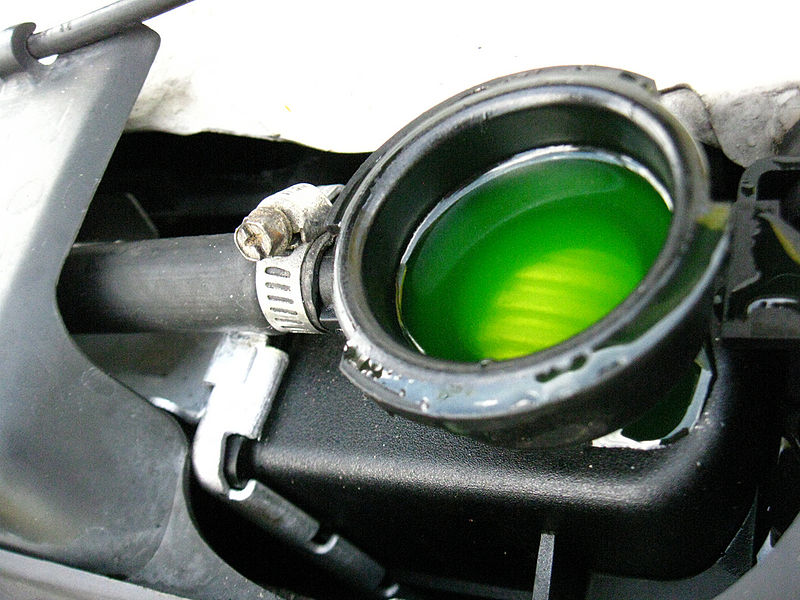
Liquid-cooled engine: How does liquid cooling work?
Between 1909 and 1919, the radial engine was eclipsed by its very similar relative, the rotary engine. However, it differs from the radial engine because the crankshaft is firmly attached to the aircraft structure. At the same time, the crankcase is connected to the propeller together with the cylinders and rotates. Simply put, the crankcase, cylinders, and propeller rotates, but the crankshaft does not.
In the First World War, rotary engines were used en masse in Allied aircraft. Most German aircraft at the time used water-cooled inline 6-cylinder engines. In the 1930s, however, the radial engine returned to the scene. During the Second World War, radial engines were mainly used in American, Japanese, Italian, and British aircraft but also appeared in German ones.
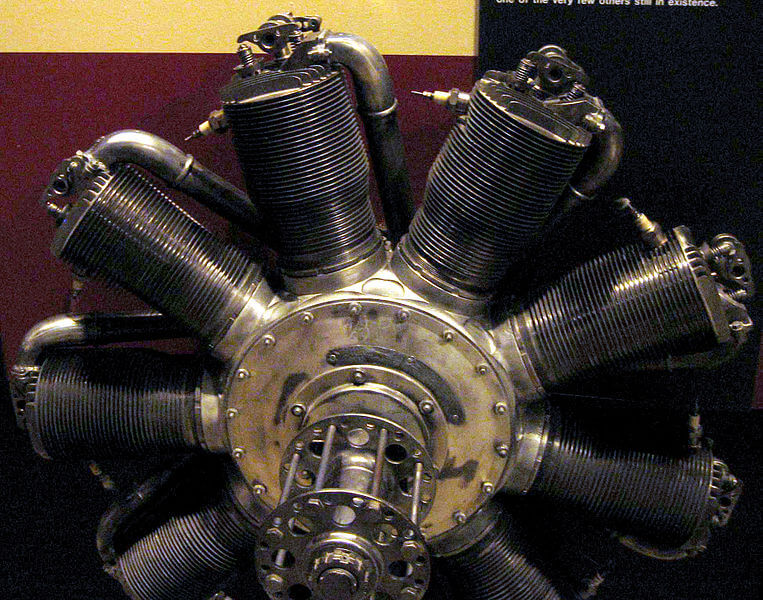
Rotary engine: What are its advantages?
The United States of America also massively deployed radial engines in tanks such as the M3 Lee, M18 Hellcat, M2 light tank, and M4 Sherman. During the Second World War, the largest marine radial engine was also built, with 16 rows, 112 cylinders, and a displacement of up to 383 liters.
The radial engine and its construction
As mentioned above, a radial engine is equipped with one crankshaft, and its cylinders are arranged in a circle (in one or more rows) perpendicular to the axis of the crankshaft, so that all cylinders make the same angle with each other.
In radial engines, individual cylinders, on which separate cylinder heads are located, are attached to the engine block and are equipped with cooling fins. This makes it possible to ensure sufficient air cooling of thermally stressed components in radial motors.
The engine block is the main supporting body of the engine, consisting of three parts: the rear, middle, and front. In the middle part, there is a crank mechanism and a cam mechanism; in the front part of the block, there is a reducer. The rear part closes the engine block. All individual cylinder sets are attached to the engine block, but the entire engine is also connected to the aircraft structure through the engine block.
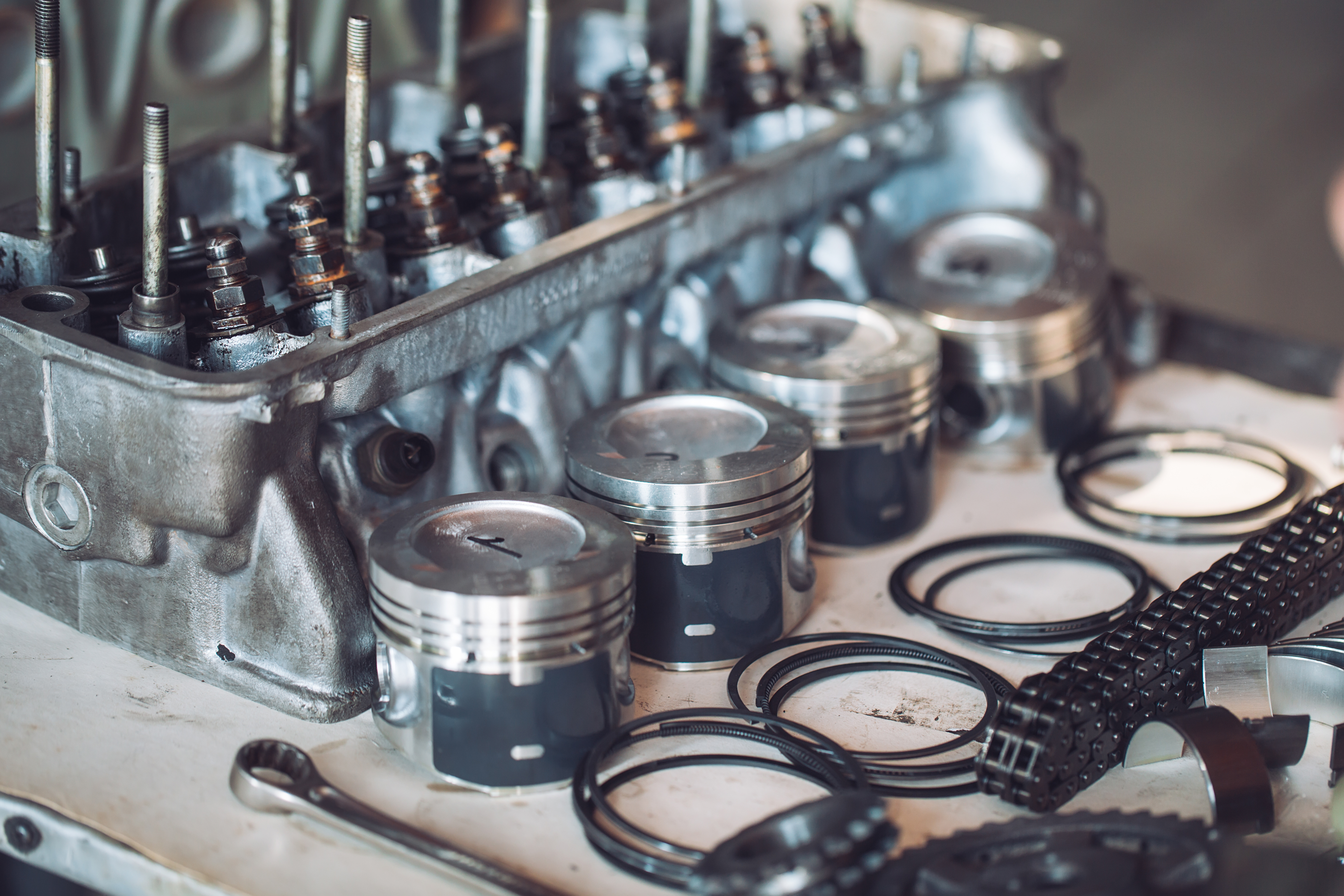
Engine Pistons: How do they work?
The radial engine pistons are connected to the crankshaft using connecting rods as in conventional piston combustion engines. However, connecting the connecting rods to the crankshaft is not the same. One piston is connected directly by the main connecting rod, which has a hanging eye, to which the connecting rods of the other pistons are attached using pins.
The radial engine uses OHV valve timing. The cams ensure the movement of the valves, but not using a camshaft, but a cam disk, which rotates with the cams more slowly and in the opposite direction than the crankshaft. The cam disk also has the same number of intake and exhaust cams.
For example, a 5-cylinder radial engine has a cam disc equipped with two intake and two exhaust cams, which rotates four times slower than the crankshaft. The camshaft is driven using a crankshaft-driven planetary gearbox. Lifters, rods, and rockers ensure the movement between the cam and the valve.
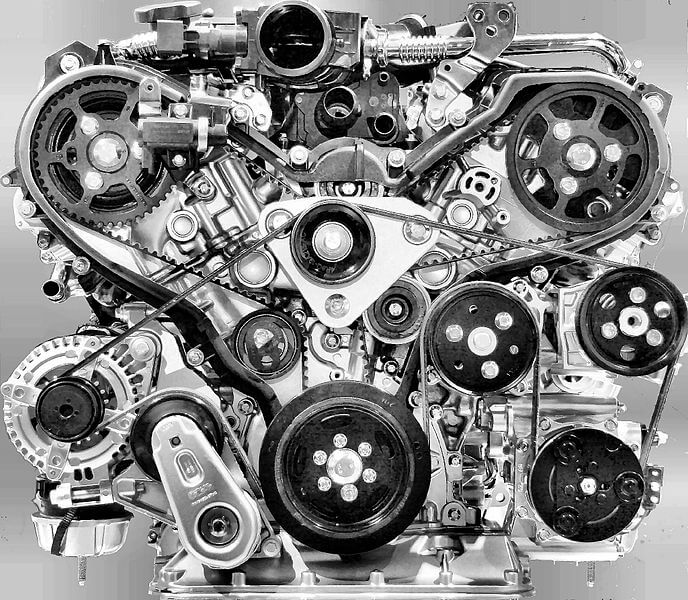
The number of cylinders of a radial engine depends on the number of working cycles of the engine. In the overwhelming majority, however, the four-stroke cycle is used. In the case of a four-stroke radial engine, the number of cylinders in each row must be odd so that the ignition comes out, which, for example, in a 5-cylinder engine, is in the order 1-3-5-2-4 and so on. However, the number of cylinders in one row can be even with two-stroke radial engines.
The basic requirements for a radial engine:
- high performance
- lowest possible weight
- smallest possible dimensions
- high reliability
- long service life
- lowest possible fuel consumption
- balanced and refined operation
- simple engine operation
- reasonable production price
The radial engine is overwhelmingly built as a petrol engine but can also be built as a diesel (diesel). The main advantages of a diesel radial engine include lower fuel consumption and lower risk of ignition.