Fuel injection: How does preparing the mixture work?
Fuel injection is a method of preparing a mixture of fuel and air for internal combustion engines. The fuel injection principle consists of injecting fuel into the intake pipe, intake channel, chamber, cylinder, or compression space through a small opening, or injector nozzle.
To create the most suitable mixture, the fuel in front of the nozzle is compressed to a higher pressure than the pressure in the space into which it is injected. Due to the higher pressure and the small size of the nozzle, the fuel is atomized during the injection, which makes it possible to accelerate the formation of the mixture.
Content
The exception is the oldest pneumatic injection system, in which fuel with unchanged pressure is fed into the combustion chamber through a nozzle using a compressed air stream. Nowadays, however, this fuel injection system is no longer used.
The injection device provides fuel injection. This is used for the transport and atomization of fuel, and its task is to ensure the supply of the exact amount of fuel, at the exact time according to the current requirements for the performance of the engine.
The injection device consists of:
- Fuel tank
- Connecting pipe
- Fuel temperature sensor
- Transport pump
- Fuel cleaners (fuel filter)
- Injection pump
- Discharge pipe
- Compressor
- Compressed air reservoir
- Compressed fuel tank
- Pressure regulator
- Injector
- Control unit
- Other components
However, not all listed components may always be present depending on the injection concept and engine type.
Transport pump:
It may not be present on all injection devices. In some old injection devices, the transport pump was replaced by a height arrangement of the fuel circuit so that the fuel tank was higher than the injection pump.
The fuel was transported from the fuel tank to the injection pump, so the force of gravity flooded it.
Compressor and compressed air tank:
These components were present only with the pneumatic fuel injection system, which, as I mentioned, is not used today.
According to the type of engine, concept, and construction of fuel injection, we distinguish:
Fuel injection for a petrol engine:
1. Indirect fuel injection
It is a method of preparing a mixture for ignition engines. With indirect injection, the fuel passes through the nozzle under pressure, which leads to a fine atomization of the fuel into small particles and ensures its rapid evaporation.
Injection and mixture formation occurs before the intake valve, pipe, or channel. Since fuel is not injected directly into the cylinder, it is called indirect injection.
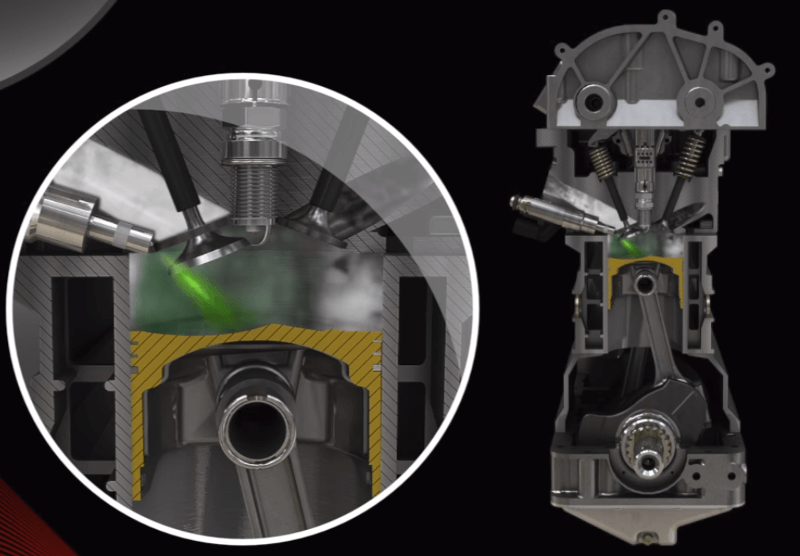
The main task of indirect injection is to create the most homogeneous mixture of fuel and air in the correct ratio. For conventional spark-ignition engines equipped with a three-way catalytic converter, the correct stoichiometric mixture is one in which the air-fuel ratio λ = 1.
2. Direct fuel injection
With direct fuel injection, the fuel is injected directly into the cylinder, which enables active control of the layered formation of the mixture. A gasoline engine with direct injection burns a homogeneous, but also an inhomogeneous (stratified) mixture.
A homogeneous mixture injects a dose of fuel λ = 1 into the combustion chamber during the intake stroke. With a stratified mixture, the fuel is injected into the stirred air during the compression stroke, which creates a locally homogeneous mixture in the area of the spark plug.
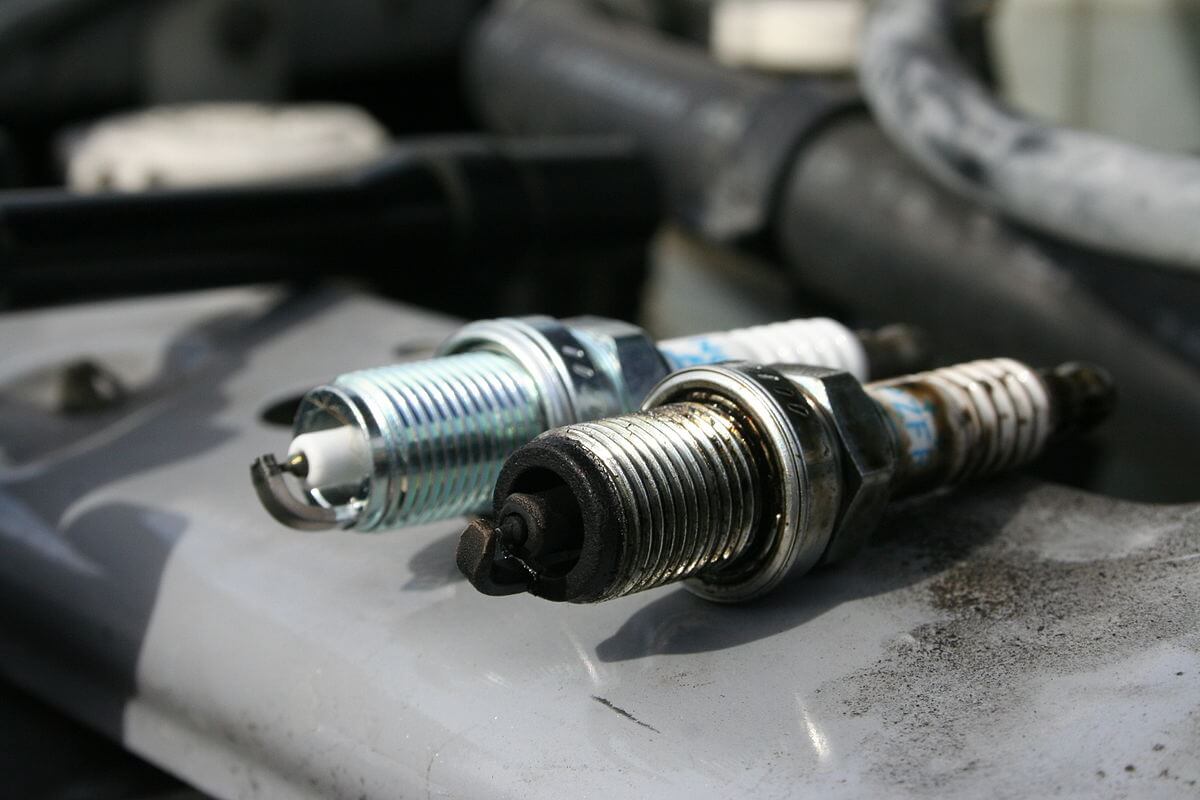
However, there is a lean mixture in the other spaces of the cylinder, and the air-fuel coefficient is, therefore, λ > 1. Combustion with an excess of air (lean mixture) makes it possible to reduce fuel consumption.
Fuel injection for diesel engines:
1. Indirect (chamber) fuel injection
With chamber injection, the fuel is injected into a chamber (created in the cylinder head), where it ignites due to high temperature and pressure and continues into the main combustion chamber.
Diesel engines with indirect fuel injection have higher fuel consumption and lower power than diesel engines equipped with direct fuel injection. However, their advantage is less demanding construction and less susceptibility to fuel quality.
2. Direct fuel injection
Fuel is injected directly into the combustion chamber with direct injection, where it ignites due to high temperature and pressure. Direct fuel injection is carried out for diesel engines using an injection system with a pressure reservoir—a common rail abbreviated as CR or the PD - Pumpe Duse system (creates high pressure directly in the injectors).
In the case of petrol engines, where the amount of mixture regulates the engine performance, fuel injection has several advantages compared to the carburetor method of preparing the mixture, such as higher engine power, lower fuel consumption, lower emissions, and even distribution of the mixture.
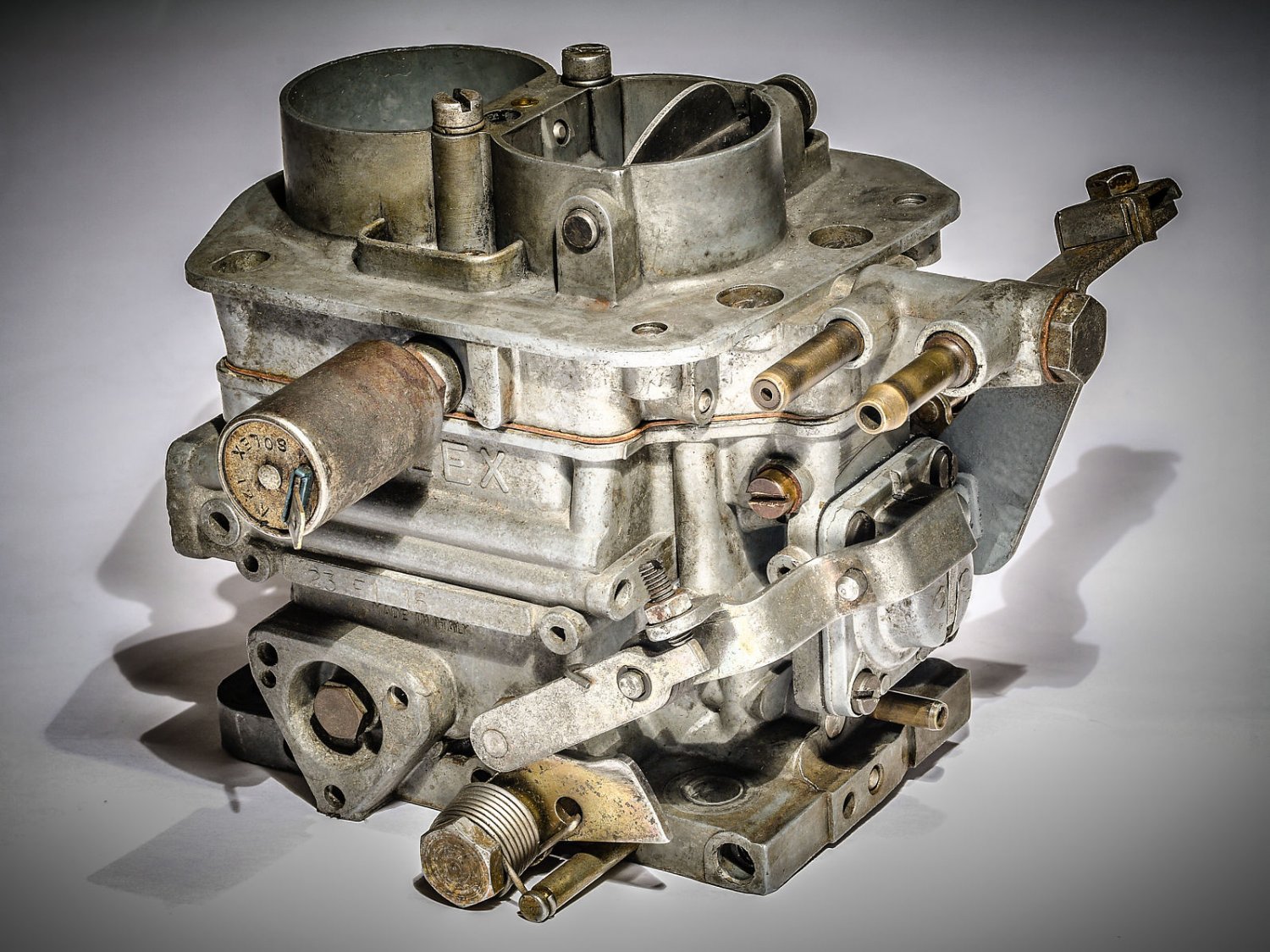
Carburetor: How does this device work?
Carburetors are intended for mixing air and fuel in the required quantity and ratio according to the engine load and its revolutions. Engine power is regulated by direct airflow control, which indirectly controls fuel flow because the carburetor mixes them in a constant ratio.
However, the diesel engine directly regulates the output by the amount of fuel, which means that carbureted diesel engines do not exist.