Air-fuel ratio: How does it affect engine performance?
An air-fuel ratio is a dimensionless number that expresses the ratio between the actual amount of air in the mixture and the theoretical amount (stoichiometric amount) of air corresponding to the fuel used. The coefficient, named in English as the Air-Fuel Ratio, is denoted by the Greek letter λ (lambda).
The coefficient defined in this way is mainly used in the field of internal combustion engines because it is a necessary parameter for the preparation of the mixture. The air-fuel ratio thus thoroughly expresses the mixture's richness level. Each fuel needs a different amount of air for its perfect combustion.
Content
- According to air-fuel ratio, we can divide the combustion mixture into
- Effect of mixture composition on engine parameters
- Combustion of a stoichiometric mixture
- Rich mixture combustion
- Lean mixture combustion
- Effect of mixture composition on engine components
- Air-fuel coefficient λ: What do the specific values mean?
For example, depending on its composition, 1 kg of regular car gasoline requires approximately 14.7 kg of air for complete combustion. For diesel, 15 to 15.5 kg of air is needed for 1 kg of fuel. Thus, if the perfect ratio between fuel and air in the mixture is maintained, the air-fuel ratio will reach 1 (λ = 1). In such a case, we speak of a stoichiometric mixture.
According to air-fuel ratio, we can divide the combustion mixture into:
- If the mixture contains exactly the stoichiometric amount of air λ = 1, it is called stoichiometric (contains the correct ratio of air for perfect combustion of fuel)
- If the mixture contains more air λ > 1, it is called lean (contains less fuel than can be burned)
- If the mixture contains less air λ < 1, it is called rich (contains more fuel than can be burned)
However, with different operating modes of the engine, the working conditions of the engine change, and thus the requirements for the amount of fuel supplied differ.
Typical operating modes of the engine in which the composition of the mixture must be adjusted are, for example:
- Cold start
- Cold engine
- Warming up the engine
- Acceleration
- Deceleration
- Idling
- Air conditioning on
- Full load
- Altitude
Effect of mixture composition on engine parameters:
Depending on the air-fuel ratio, under the same engine conditions, the following are affected:
- Fuel consumption
- Engine performance
- Amount of emissions
- Evenness of engine operation
- Engine heat load
All these parameters depend on the composition of the mixture. However, the actual mixing ratio of the mixture differs significantly from the theoretical one. The temperature, speed, and load of the engine determine it.
The mixture ratio at which performance, emissions, and consumption reach the best values is unique for each engine and operating mode.
Combustion of a stoichiometric mixture:
In theory, emissions should not occur when burning a stoichiometric mixture. In practice, however, the situation is different. Due to insufficient homogenization of the fuel and its interaction with other substances (engine oil, impurities in the fuel, influence of nitrogen from the air) and the short time in which the combustion process must occur, emissions formation occurs.
Since the engines of ordinary cars are mainly operated at partial load, they are designed for this operation so that their operation is as efficient as possible in this mode. In this mode of operation, working with a stoichiometric mixture is a suitable compromise between performance, fuel consumption, and the amount of emissions produced.
In addition, the engines of today's cars must first meet the emission limits, so using a stoichiometric mixture (λ = 1) seems to be the most appropriate because that is when the catalytic converter has maximum efficiency. The engine is, therefore, the most ecological.
Rich mixture combustion:
When burning a rich mixture, combustion takes place faster, and the air-fuel ratio reduces the maximum temperature by evaporation, which ensures internal cooling of the cylinder group, which in turn makes it possible to increase the engine's compression ratio.
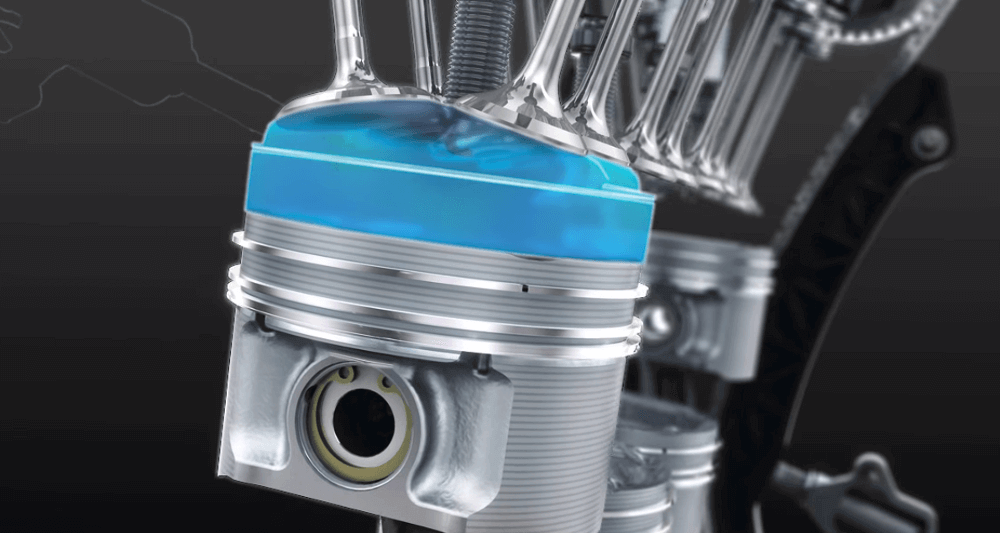
Thanks to this, the engine's power increases, but at the same time, its consumption also increases, because not all the fuel is burned perfectly, and part of its energy remains unused.
All other parameters go aside in this mode, and performance becomes the main parameter. The mixture is thus enriched (λ < 1) to achieve the highest possible engine performance.
Lean mixture combustion:
The lowest consumption is achieved in the lean mixture combustion mode; thus, the air-fuel ratio reaches the value (λ > 1). When the engine is under low load, the performance is not interesting, so the priority becomes fuel consumption.
In such a case, setting a slightly lean mixture (λ > 1), which achieves the greatest fuel savings, is the clear choice for this mode.
Effect of mixture composition on engine components:
A rich mixture has a significant effect from the point of view of engine protection, because the fuel that does not burn removes the temperature from the combustion chamber through its evaporation, thereby ensuring effective cooling of the combustion chamber.
The cooling effect increases with the richness of the mixture, which is especially important for extremely stressed engines. This is why a rich mixture is burned at maximum engine load.
However, there is no need to overdo it with the richness of the mixture, because unburnt fuel washes the oil film from the walls of the cylinders, which increases the risk of piston seizing. In addition, this increases the formation of carbon, the deposits of which prevent the removal of heat from the combustion chamber.
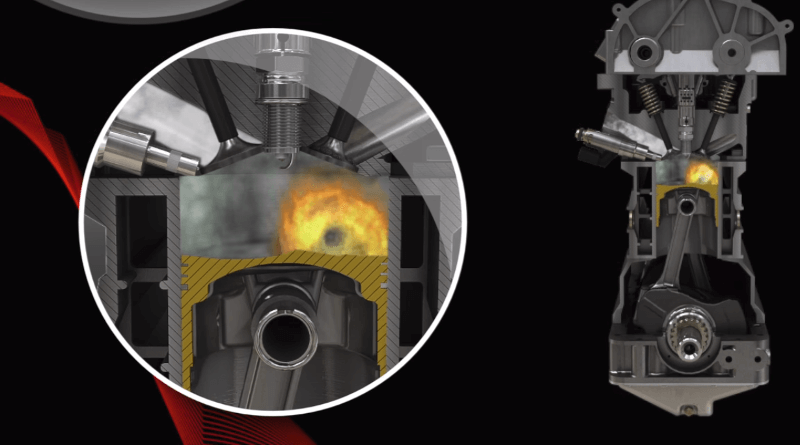
When burning a lean mixture, there is a risk of the absence of internal cooling, which can lead to a thermal overload of some engine components, for example, pistons, valves, and spark plugs. However, higher local temperatures in the cylinder significantly increase the risk of detonation combustion.
Internal fuel cooling can only be used for spark-ignition engines because they can work with a rich mixture due to a longer time for its preparation (fuel enters the cylinders together with air or is injected into the cylinder during the intake stroke).
In combustion-ignition engines, where fuel is injected into the cylinder, and the combustion phase begins simultaneously, a rich mixture that does not mix well with the air would lead to excessive smoke. This means that even at thefull load of the diesel engine, the air-fuel ratio is only close to the stoichiometric mixture so that the highest possible performance is achieved.
Air-fuel coefficient λ: What do the specific values mean?
- <0.5- the lower limit of flammability (rich mixture), the mixture of fuel and air is no longer flammable
- < 1 - rich mixture, lack of air, increased power and torque
- 0.9 - the highest torque, good engine operation, worse specific fuel consumption
- 0.9 to 1.1 - theoretically suitable mixture of fuel and air
- >1 - lean mixture, excess air, fuel saving, economical operation
- 1.3 to 1 .5 - the upper limit of the flammability of the mixture (lean mixture), the mixture of fuel and air is no longer flammable
- 1.6 to 1.7 - the upper limit of the flammability of the mixture for engines with a stratified mixture
However, in general, a properly functioning engine at the correct temperature and load burns:
Diesel engine - burns an inhomogeneous (stratified) mixture with a high excess of air. The mixture is lean, has a larger proportion of air than would belong to a certain amount of fuel, and the air-fuel ratio is, therefore, λ > 1.
Petrol engine with indirect injection - burns a homogeneous mixture. The coefficient of the proportion of air is λ = 1, and such a mixture is called stoichiometric.
Gas engine with direct injection - burns homogeneous but non-homogeneous (layered) mixture. A homogeneous mixture injects a fuel λ = 1 dose into the combustion chamber during the intake stroke.
A stratified mixture injects fuel into the swirled air during the compression stroke, creating a locally homogeneous mixture in the spark plug area. However, there is a lean mixture in the other spaces of the cylinder, and the air-fuel coefficient is, therefore, λ > 1.