Direct injection petrol engine: How does it work?
A spark-ignition engine with direct fuel injection is a type of piston combustion engine that, unlike a spark engine with single-point or multi-point fuel injection or carburetor method of mixture preparation, does not burn only a homogeneous mixture.
Fuel is injected directly into the cylinder during the intake or compression stroke using the injection valves, atomizing and vaporizing it before the spark plug ignites the mixture with a spark.
Content
- Direct injection petrol engine function
- 1. Mode with a homogeneous mixture
- 2. Mode with the homogeneous operation and lean mixture
- 3. Mode with the homogeneous operation and layered filling
- 4. Mode with homogeneous operation and protection against engine knocking
- 5. Layered mix mode
- 6. Mode with the stratified mixture and catalytic converter heating
- Combustion of stratified mixture
- Construction solution of layered mixture preparation
- Advantages of petrol engine with direct injection
- Disadvantages of petrol engine with direct injection
Direct injection petrol engine function
A spark-ignition engine with direct fuel injection creates a working mixture of fuel and air only in the combustion chamber, which means that it is an internal creation of the mixture.
With this method of preparing the mixture, there are no condensation losses caused by the condensation of fuel on the walls of the intake pipe. Also, the timing of the fuel injection, as well as the amount of fuel injected, is very precise, thanks to which fuel consumption is reduced.
Depending on the load, revolutions, engine temperature, and other parameters, the spark-ignition engine with direct injection works in different modes with different mixture compositions:
- Mode with a homogeneous mixture
- Mode with the homogeneous operation and lean mixture
- Mode with the homogeneous operation and layered filling
- Mode with homogeneous operation and protection against engine knocking
- Layered mix mode
- Mode with the stratified mixture and catalytic converter heating
1. Mode with a homogeneous mixture
In this mode, the fuel is injected already during the intake stroke, thanks to which sufficient time is achieved to create a uniformly composed mixture. In this case, it is a stoichiometric mixture λ = 1, in which the fuel is completely burned, in its entire volume.
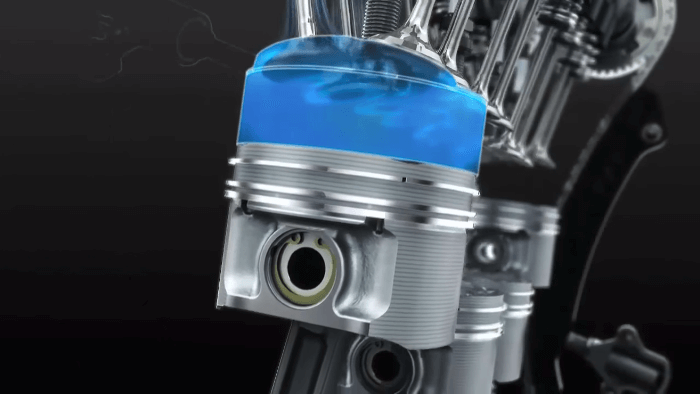
Stoichiometric mixture: What type of mixture it is?
In this gasoline engine mode with direct injection, the course of combustion, fuel consumption, emissions, and other parameters are not very different from a gasoline engine with multi-point injection.
This mode is universal, regardless of engine speed, temperature, or load. However, this would deprive the engine of the advantages of layered filling, which is why this mode is mainly used at high engine speeds and loads.
2. Mode with the homogeneous operation and lean mixture
In this mode, the gasoline engine with direct injection achieves lower fuel consumption than in the mode with a homogeneous mixture due to a higher filling efficiency, because the throttle valve is opened more than in the mode with a homogeneous mixture.
The composition of the mixture in this regime is 1 < λ < 2.
3. Mode with the homogeneous operation and layered filling
In this mode, the air-fuel ratio reaches the value λ > 2, and the fuel is injected twice. During the first injection, which takes place during the intake stroke, about a quarter of the fuel charge per cycle is delivered to the combustion chamber, which creates a homogeneous mixture.
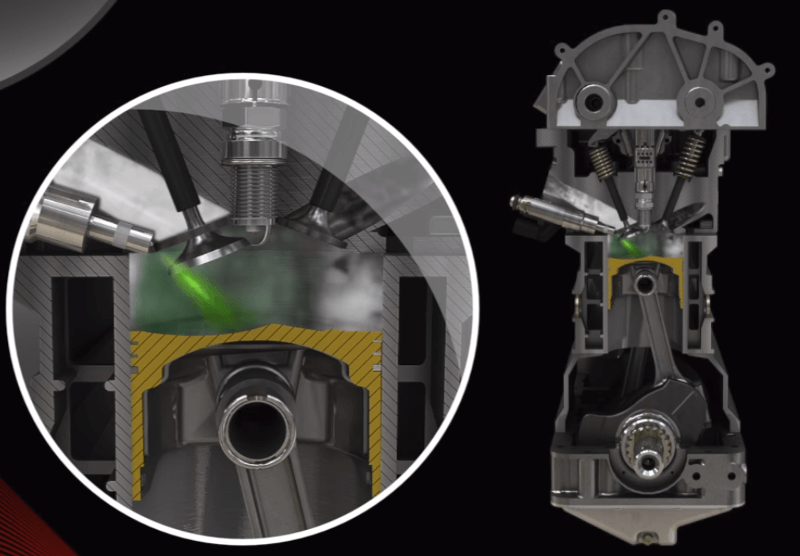
The rest of the fuel is injected only during the compression phase, while its task is to create a well-igniting richer mixture in the area of the spark plug.
4. Mode with homogeneous operation and protection against engine knocking
This mode is primarily intended for high loads at low engine speeds when engine knocking could occur. In this mode, double fuel injection is again used as in the previous mode.
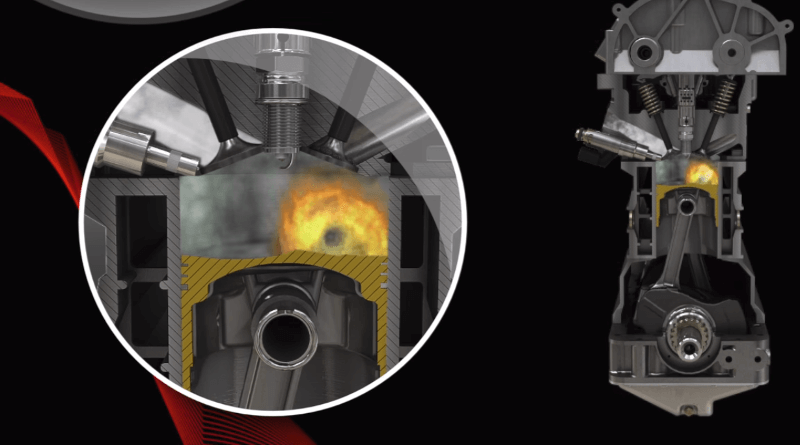
A second batch of fuel is thus injected during the compression phase, reducing the temperature and pressure in the combustion chamber, thus preventing detonation combustion.
5. Layered mix mode
In this mode, fuel is injected into the combustion chamber during the compression stroke just shortly before the spark plug ignites the mixture with a spark.
The fuel does not have time to mix well with the air, and the engine works with a lean mixture, where the air-fuel ratio is λ > 1, but there is a well-ignitable mixture in the area of the spark plug, which is ignited by a spark.
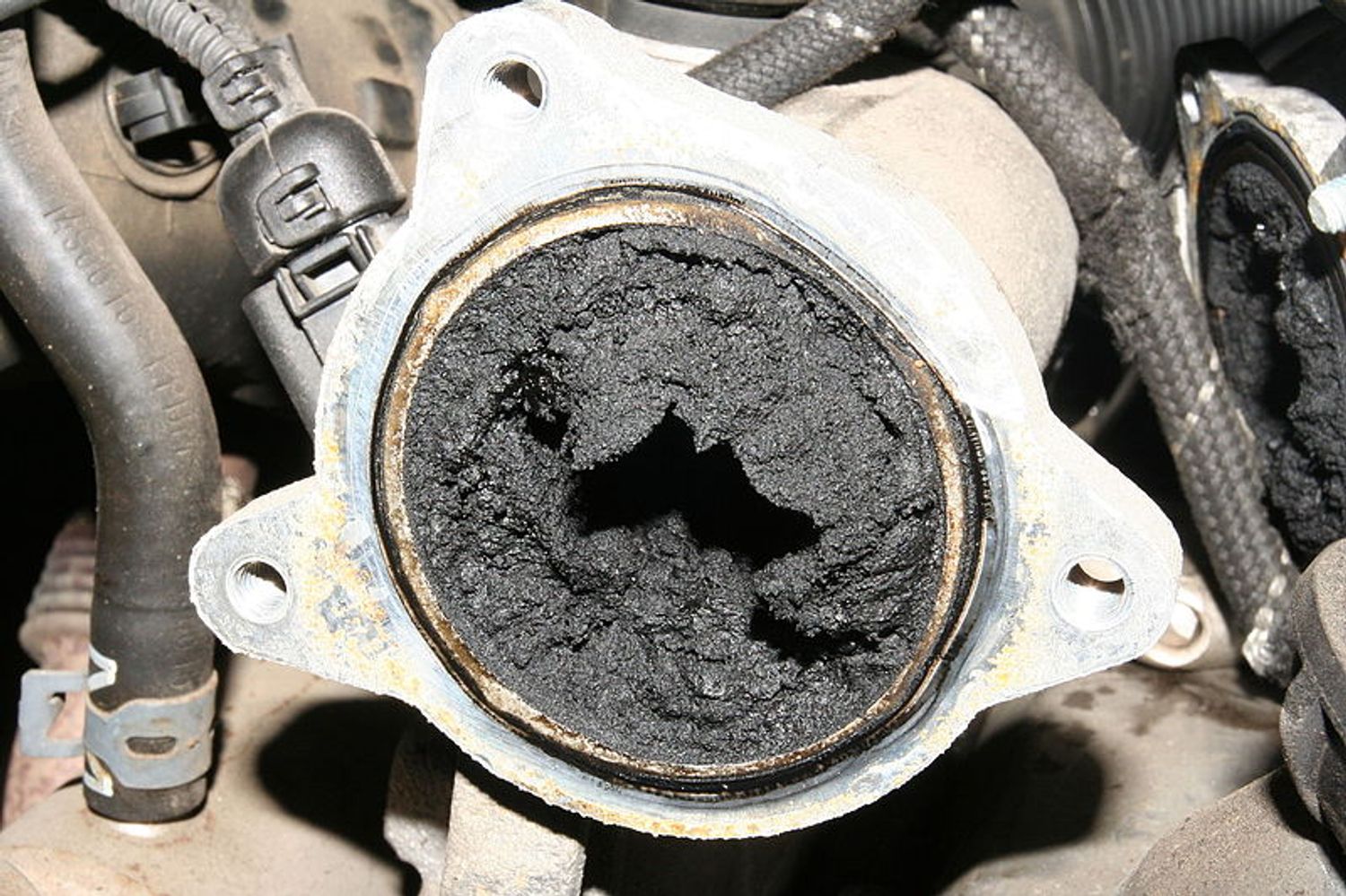
EGR valve: What happens if it doesn't work properly?
In this mode, recirculation of exhaust gases from previous cycles, provided by the EGR valve, is also intensively used.
Simply put, there is a well-ignitable mixture in the spark plug area, and in other parts of the combustion chamber, there is a lean mixture of exhaust gases from previous cycles. The layered mixture mode is more suitable for lower to medium engine speeds.
6. Mode with the stratified mixture and catalytic converter heating
This mode is used only to heat the catalytic converter to its operating temperature. The engine operation principle during this mode is the same as in the previous mode except for one difference.
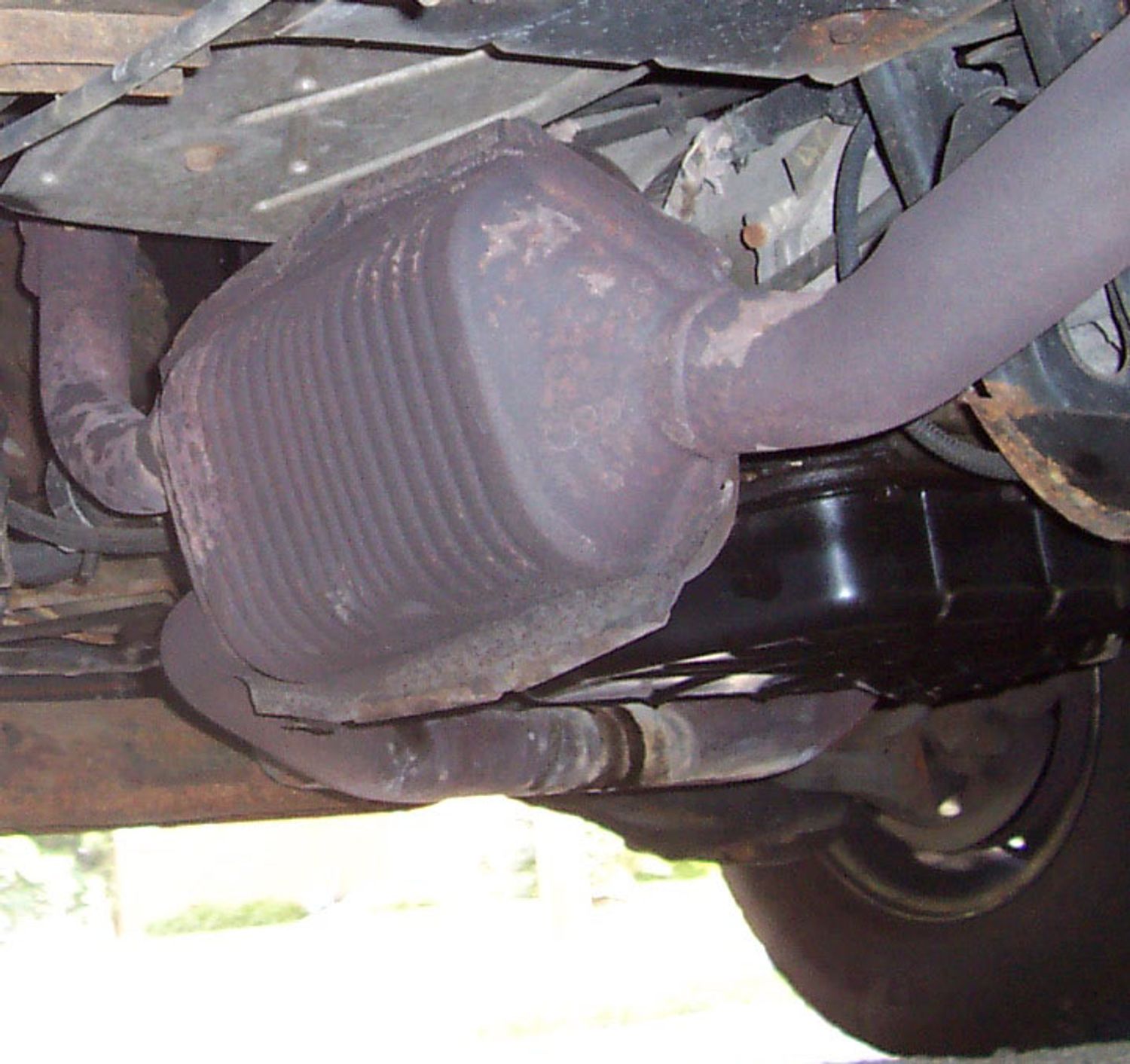
During the expansion, one more fuel is injected into the combustion chamber, due to which the temperature in the exhaust pipe increases and thus also the temperature of the catalytic converter.
Combustion of stratified mixture
To ensure the quality of the combustion process with a stratified mixture, it is necessary to harmonize the shape of the combustion chamber, the bottom of the piston, the mutual location of the spark plug and the injector, but also the speed of the airflow, the direction, the shape and the right moment of the injection of the fuel beam.
Combustion of a layered mixture can therefore be divided into:
- Combustion guided by a fuel beam - the fuel must be injected near the spark plug
- Combustion guided by the combustion chamber walls - the fuel is injected into the air stream, which, thanks to the appropriate shape of the wall cylinders and the bottom of the piston, will bring the mixture of fuel and air to the spark plug at the right time.
Construction solution of layered mixture preparation:
- Direct injection with spark plugs and injectors close together
- Direct injection with spark plugs and injectors far apart
1. Direct injection with spark plugs and injectors close together
In this design solution of layered mixture preparation, beam-guided combustion is used. The injector therefore injects fuel into the combustion chamber, while the fuel beam directly hits the spark plug electrodes area.
Advantages:
- The large layering of the mixture due to spraying around the candles, thanks to which the mixture around them is always sufficiently rich, but in the rest of the combustion space, there is an extremely lean mixture.
Disadvantages:
- It takes a short time to prepare the mixture, which reduces its quality
- Dependence of the beam shape on compression pressure
- Problems with cold engine start
- High demands on injectors
2. Direct injection with spark plugs and injectors far apart
In this structural solution of layered preparation of the mixture, combustion guided by the walls of the combustion chamber is used.
Advantages:
- Longer time to prepare the mixture, which increases its quality
- Better mixing of fuel and air (less stratification)
Disadvantages:
- The stratification of the mixture is aided by the shape of the combustion chamber
- In case of large turbulence in the combustion chamber, the required stratification of the mixture is not achieved
Advantages of petrol engine with direct injection
- Higher engine performance
- Lower fuel consumption (15 to 30%)
- Precise fuel dosing
Disadvantages of petrol engine with direct injection
- Lower reliability
- More demanding construction
- More nitrogen oxides and solid particles are produced when burning an inhomogeneous mixture.